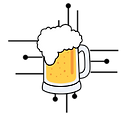
Brüboiz

Brüboiz
Automated Nano-Brewery
The Brüboiz’ automated brewery control system brings the complete brewing experience to the avid home brewer. From grain to fermentation, our system will allow anyone to create commercial grade brews effortlessly.


The project is focused around the design and development of an industrial style control cabinet for a nano-brewery. This includes hardware to power the system, as well as the software to manage the brew process automatically. The end goal is to upgrade our client’s prototype brewing system to a robust and streamlined finish.
Features
Fully Automated Brewing
Using our user interface the user can select their favorite brew recipe or select their own parameters. Then they only need to put the corresponding grain into the hopper and press ‘start’.
Touchscreen HMI
Our integrated touchscreen is the focal point of the project. It is the user’s brewing portal, from which they will control the brewing process.
PLC Control
The automated brewery control system uses Arduino’s Opta Wi-fi PLC (Programmable Logic Controller) as its central processor. This gives the system modern connectivity features, without the cost of ‘big industry’ controllers.
Enclosure
Our system hardware is housed in a robust metal enclosure. The enclosure is designed to offer protection against dust and water, keeping the electronics safe during brewing or cleaning.
Hardware
Hover over hardware components to get a description of their purpose within our project.

Buck Converter:
Converts 24VDC to 8VDC to run servo motors.
Arduino OPTA PLC:
The PLC is the "brain" of the project. It controls inputs and outputs of the system, and is manipulated via the HMI.
PLC Digital Module:
The digital module actuates relays and solenoid valves.
PLC Analog Module:
The analog module reads temperature sensor data and outputs PWM signals to servo valves.
DC Power Supply:
The DC power supply converts 120 VAC to 24 VDC to run the PLC and HMI.
120 VAC Breaker:
The 120 VAC breaker offers circuit protection from grinder startup current.
Solid State Relays:
The SSR's turn on high power components like the heaters and grinder.
Terminal Strips:
The terminal strips are used to organize wire runs and to streamline troubleshooting.
240 VAC Breaker:
The 240 VAC breaker is used for circuit protection for the heater current draw.
Meet The Team
Our journey began when our partner, Black Beard Brewing, approached Camosun College in hopes of developing their prototype brewery setup. To meet this challenge, four like-minded individuals came together, bringing their love of beer and engineering. Thus, the Brüboiz were born.

Lukas Koch:
Lukas brings the same passion he has for sailing to the Brüboiz team. He is in charge of PLC programming and has shown an aptitude for parts selection and research. Lukas has been instrumental in translating Black Beard Brewing’s recipes into a software process.
Maddox Brown:
An aficionado in bouldering and video games, Maddox is the Brüboiz AutoCAD expert. He has been instrumental in project design choices, such as the layout of the touchscreen menus, and is largely responsible for this very webpage.
Alex McGill:
Alex is a hockey fan and all-around outdoors enthusiast. His specialty within the Brüboiz is the implementation and design of our HMI touchscreen menus. He also worked heavily with Lukas on setting up communications between the PLC and HMI.
Cameron Richmond:
Cameron enjoys music and dog walking, and is the Brüboiz main editor and client coordinator. He has assisted both Lukas with part selection, as well as Maddox with AutoCAD. Cameron has acted as the main link between the Brüboiz and Black Beard Brewing.
The Brüboiz team
Hover over each boi
Our Client

Ben Haber

Matt Buie